Extrusión Reactiva (REX)
Procesos > ► Extrusión
Extrusión Reactiva (REX)
La Extrusión Reactiva (Reactive Extrusion o REX en inglés) se ha presentado en los últimos años como una tecnología puntera para la síntesis y modificación química de polímeros. El proceso de REX está basado en el empleo de una extrusora a modo de reactor químico, lo que permite unificar el proceso de polimerización y/o modificación del polímero y el de granulación en una única etapa. A partir de este desarrollo es posible obtener el material apto para su posterior transformación mediante diferentes procesos, como son el proceso de inyección y el de extrusión de plásticos. Generalmente, la extrusión reactiva se lleva a cabo en extrusoras de doble husillo corrotantes (Twin Screw extruder TSE en inglés), debido a su alta capacidad de mezcla y versatilidad en el diseño del proceso. En estas extrusoras, los monómeros y/o polímeros y otros reactivos alimentan de forma continua a la extrusora, donde funden, se mezclan y reaccionan a lo largo de la misma de forma similar a un reactor tubular. Finalmente, se obtiene el polímero o material compuesto en estado fundido que se enfría y corta en forma de granza para su transformación posterior. Otra gran ventaja es que la extrusión reactiva permite llevar a cabo reacciones de polimerización en ausencia de disolventes, o empleando una cantidad mínima de éstos en comparación con procesos de polimerización por lotes. Esto permite un ahorro considerable al evitarse el uso y posterior proceso de extracción y recuperación del disolvente. La extrusión reactiva está indicada para reacciones rápidas, donde el proceso de reacción se puede llevar a cabo en el rango de tiempos de residencia típicos de estas extrusoras (de 1 a 15 minutos). Para ello es absolutamente necesario realizar un estudio previo de la cinética de reacción, de forma que se pueda acoplar al tiempo de residencia de la extrusora mediante un diseño del proceso a medida. Las reacciones más comunes que pueden ser llevadas a cabo mediante el proceso de extrusión reactiva son las siguientes:
- Poliadición; obtención de poliuretano termoplástico (TPU) de diferente dureza.
- Policondensación; síntesis de poliésteres como el tereftalato de polietileno (PET), tereftalato de polibutileno (PBT) y poliamidas.
- Reacciones de injerto y funcionalización; funcionalización de poliolefinas (principalmente polietileno y polipropileno) con anhídrido maleico y otros monómeros acrílicos (por ejemplo, PE-g-MAH, PP-g-MAH, PE-g-AA, PE-g-GMA).
- Compatibilización; obtención de mezclas de polímeros o blends a partir de poliésteres, biopolímeros con compatibilizantes, alargadores de cadena.
- Proceso de esterificación parcial de EVA a partir de la sustitución del grupo acetato por alcohol.
- Entrecruzamiento; formulación de elastómeros termoplásticos a partir de poliolefinas, cauchos, aceites y agentes de entrecruzamiento.
- Reticulación de polietileno mediante vinil silanos y peróxidos.
- Degradación controlada; para reducción de la viscosidad del PP reciclado a medida.
- Polimerización iónica; obtención de ácido poliláctico (PLA) y de poliamida 6 (PA6) mediante reacciones de polimerización de apertura de anillo.
- Glicólisis. Reciclado químico del PET.
- Hidrólisis. Obtención de polioles y aminas a partir de poliuretanos (PU) y poliuretanos termoplásticos (TPU).
- Saponificación. Síntesis de ionómeros elastoméricos a partir de copolímeros acrílicos de etileno (EMA, EBA).
Proceso
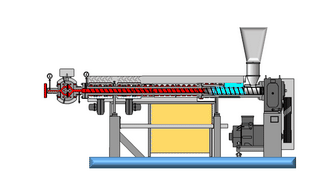
Después, la mezcla reactiva es transportada a través del extrusor y la reacción se lleva hasta el grado de conversión deseado. En este punto, y después de haber removido los subproductos volátiles formados, el polímero en estado fundido es bombeado a través de un dado, posteriormente es enfriado y una vez en estado sólido es peletizado para su posterior transformación. Así, la producción y el procesamiento se pueden integrar en una sola etapa. De esta forma, las reacciones que previamente requerían diversos equipos de grandes dimensiones, particularmente en las operaciones por lotes, actualmente se pueden realizar de una manera continua, en forma eficiente, mediante extrusión reactiva.
Características de los Extrusores empleados para Procesado Reactivo
Un proceso típico de extrusión reactiva implica el siguiente procedimiento: Los reactivos se alimentan a través de la tolva principal a la extrusora de doble tornillo, donde los reactivos se calientan para iniciar la reacción química. El perfil de temperatura, el uso de activadores y catalizadores y el tiempo de residencia del material en la extrusora determinan la velocidad de reacción y el progreso de la reacción. En consecuencia, el rendimiento, la longitud de la extrusora y la velocidad del tornillo limitan el grado de polimerización. De lo contrario, la polimerización se puede detener específicamente mediante la desactivación de los grupos terminales reactivos para lograr una baja viscosidad. La adición de reactivos sólidos, líquidos o gaseosos es posible en casi cualquier posición de la extrusora. No obstante que se pueden utilizar extrusores monohusillo y doble husillo para los procesos REX, los doble husillo son los más adecuados. Las principales razones para ello son el mejor control que se obtiene sobre la distribución del tiempo de residencia (RTD) y el grado de mezclado, y su capacidad superior de transferencia de calor y de masa; contando además con la ventaja de tener un diseño modular, que facilita el ensamblado y permite que la geometría del extrusor sea optimizada para un objetivo especifico. Aunque los tiempos de reacción razonables para la extrusión reactiva están en el intervalo de unos segundos a veinte minutos como máximo, el proceso podría ser técnicamente posible fuera de este intervalo pero probablemente no será económicamente rentable. Este tipo de extrusores presentan innumerables ventajas cuando se utilizan en el procesado reactivo, entre las que destacan:
- Un procesado continuo
- Un excelente grado de dispersión y distribución del mezclado
- Un buen control de la temperatura y buena homogeneización térmica
- Un buen control sobre la distribución del tiempo de residencia
- Una mejora en la relación superficie/volumen
- Un fácil bombeo del producto
- La iniciación de reacciones de manera secuencial
- La polimerización sin disolventes
- La posibilidad de llevar a cabo la reacción bajo presión
- La remoción de monómero residual y de subproductos por medio de venteo
- Costos bajos de producción
Más económico y ecológico: r extrusión eactive requiere menos inversión de capital y ofrece un buen rendimiento medioambiental con un menor consumo de energía en comparación con los procesos equipadas con reactores discontinuos. Los sistemas reactivos también son más compactos y, por lo tanto, requieren menos espacio. Además, la capacidad de estas máquinas para crear continuamente nuevas capas superficiales de material permite mejorar el mezclado y los problemas de transferencia de calor y de masa provenientes del drástico incremento en la viscosidad del sistema de polimerización. También en un sistema REX, se elimina el tiempo de post reacción requerido para la remoción de los productos puesto que el transporte de los materiales y la reacción ocurren de manera simultánea. De esta manera, se evitan largas exposiciones del polímero a altas temperaturas que puedan causar su degradación. Además en una reacción, se requiere de la remoción de materiales volátiles tales como - monómero sin reaccionar, subproductos, o disolventes del catalizador o de los reactivos. En REX, estos pueden ser removidos mediante el uso de un puerto de venteo.
La extrusión reactiva (REX) presenta interesantes ventajas:
- dado que la reacción se lleva a cabo en estado fundido, no se requiere disolvente
- contrariamente a los reactores discontinuos, una extrusora puede trabajar con muy viscosos productos
- las extrusoras (es decir, las extrusoras de doble tornillo) pueden ser muy flexibles (por ejemplo, permitiendo la adición secuencial de los ingredientes de la reacción, tales como monómero, polímero, agua, solvente, reactivo, etc.) y fácil de usar debido a la independencia entre la velocidad de alimentación y la velocidad del tornillo
- se puede acoplar fácilmente a los equipos posteriores, para dar forma o peletizar. Naturalmente, la extrusión reactiva también tiene algunas limitaciones
- el tiempo de residencia en una extrusora suele ser corto (normalmente, del orden de unos minutos). Por lo tanto, incluso si los valores de temperatura y concentración de reactivos son más altos en la masa fundida que en la solución, las reacciones deben ser lo suficientemente rápidas
- Las reacciones altamente exotérmicas son difíciles de controlar, debido a la baja capacidad de enfriamiento de las extrusoras (además, esta capacidad disminuye al aumentar el tamaño de la máquina).
Por el contrario, estos presentan las siguientes limitaciones:
- El mezclado se dificulta a bajas viscosidades
- Existe poca transferencia de calor del sistema hacia los alrededores
- La dificultad en el manejo de reacciones altamente exotérmicas
- Alto costo para tiempos de reacción largos
En polimerizaciones altamente exotérmicas realizadas por REX es necesario remover tanto el calor de reacción como el generado por el mezclado para mantener bajo control la temperatura. A escala comercial se puede considerar que es una operación adiabática puesto que la transferencia de calor a través del extrusor es notoriamente pobre, especialmente por conducción a través de las paredes del barril. Finalmente, el criterio para evaluar apropiadamente el sistema en donde se va a realizar la reacción debe incluir: el procesado, las propiedades del material y consideraciones económicas.
Tipos de Reacciones realizadas por Extrusión Reactiva
Reacciones de fase homogénea
- Polimerización a granel
- Modificaciones químicas de polímeros: injerto, reticulación, funcionalización, despolimerización, etc.
- Reacciones en fase líquida en química orgánica clásica
Reacciones de fase heterogénea
- Sistemas líquido-líquido de dos fases, incluido el procesamiento de caseína a caseinato, saponificación (aumento de la viscosidad según la tasa de conversión)
- Sistemas sólido-líquido de dos fases, que incluyen digestión alcalina de lignocelulósicos, blanqueo de celulosa y separación sólido-líquido, etc.
Reacciones enzimáticas
- Hidrólisis de biopolímeros (almidón y proteínas)
Los tipos de reacciones químicas que han sido efectuadas mediante extrusión reactiva pueden ser clasificados en seis categorías :
Polimerización en masa
Preparación de polímeros de alto peso molecular a partir de:
- Monómeros o prepolímeros de bajo peso molecular
- A partir de mezclas de monómeros o monómero y prepolímero
Reacciones de injerto
Formación de polímeros injertados o copolímeros a partir de la reacción de un polímero y un monómero.
Formación de copolímeros
Reacciones de dos o más polímeros para formar tipo escalera copolímeros al azar, injertados, o en bloque a través de enlaces jónicos o covalentes.
Reacciones de acoplamiento
Reacción de un polímero con un agente de o entrecruzamiento acoplamiento polifuncional para aumentar el peso molecular mediante extensión de cadena o ramificación.
- Reacción de un polímero con agentes de condensación para aumentar el peso molecular por medio de extensión de cadena
- Reacción de polímeros con agentes de entrecruzamiento
Degradación controlada
Degradación de un polímero de alto peso molecular para disminuir el peso y obtener un producto con una distribución controlada de pesos moleculares.
Funcionalización
Introducción de grupos funcionales a la cadena principal.
Modificación de un grupo funcional
Modificación de grupos funcionales existentes.
Extrusoras
El proceso de extrusión reactiva utiliza un extrusor-reactor continuo (principalmente un extrusor de doble tornillo co-rotativo), con capacidades de mezcla excepcionales a nivel molecular. Este diseño de extrusora-reactor está idealmente adaptado a reacciones químicas en medios viscosos (viscosidad aparente> 100 Pa.s y / o viscosidad variable), con un buen control tiempo-temperatura. Las extrusoras de doble husillo co-rotativas entrelazadas son las más utilizadas en la extrusión reactiva, porque presentan muchas ventajas en comparación con las extrusoras de un solo husillo:
- tienen geometría modular, es decir, es posible construir el tornillo perfil y la configuración del cañón que son más adecuados a la reacción para desarrollar;
- se alimentan de hambre, es decir, la velocidad de alimentación se controla por volumen o alimentador (es) gravimétrico. En consecuencia, los tornillos funcionan principalmente parcialmente llenado, lo que conlleva algunos beneficios adicionales: i) es posible insertar a lo largo del barril diferentes puertos de alimentación, ya sea para líquidos o para sólidos
- la desvolatilización es fácil en zonas con una baja proporción de llenado, iii) la el perfil del tornillo se puede dividir en sucesivas secciones independientes, con funciones especializadas (alimentación y fusión de polímeros, inyección de reactivos, mezcla, desarrollo de la reacción, desvolatilización, bombeo y modelado ...) y iv) el tiempo de residencia y el nivel de las tensiones termomecánicas son relativamente fáciles de controlar
- tienen capacidades de mezcla superiores, tanto en distributiva como términos dispersivos. La mezcla se puede controlar mediante la geometría de ciertos secciones de tornillo (en general, bloques de discos de amasado escalonados) y por las condiciones de funcionamiento
- los tornillos pueden girar a altas velocidades (hasta más de 1500 rpm), lo que promueve altos niveles de dispersión garantizando un alto tasas de producción.
Hoy en día, muchos sistemas de polímeros se fabrican industrialmente utilizando un proceso de extrusión reactiva:
- después de la iniciación en un prepolimerizador (reactor discontinuo), el estireno suele polimerizado en una extrusora. Poliésteres, poliamidas o poliacrilatos, también se puede producir por extrusión reactiva
- Los polímeros existentes pueden modificarse químicamente para ofrecer nuevas propiedades. Por ejemplo, el anhídrido maleico se puede injertar sobre polipropileno. Otras modificaciones, como reacciones de intercambio o modificación de grupos funcionales, también se pueden realizar mediante extrusión reactiva
- la degradación del polipropileno por peróxidos se utiliza comúnmente para controlar la distribución del peso molecular y, por tanto, la propiedades reológicas
- las mezclas de polímeros inmiscibles se pueden compatibilizar de manera eficiente in situ durante la composición, mediante una reacción interfacial
- los elastómeros termoplásticos se obtienen por vulcanización dinámica,donde el elastómero se dispersa y vulcaniza en un termoplásticomatriz.